AIM – Bar Solder
Zero defect wave soldering requires consistent solder quality. Contaminants and high oxide levels in bar solder can result in a variety of wave soldering defects such as bridging, projections, and poor wetting. To avoid these issues, AIM’s low drossing solder bar alloys provide a high purity product exceeding IPC, JEDEC and IEC requirements.
AIM Electropure™ bar solder is processed from high-quality, virgin metals in a proprietary method that removes contaminants and reduces dissolved oxides. AIM’s Electropure™ technique results in an extremely pure, low-drossing solder bar that increases throughput and decreases defects.
Key Features
- Low Oxide Content
- Reduces Defects Such as Bridging and Icicling
- Lower Surface Tension than Competitive Brands
- Available in Extruded, Cast, and Margash Bars
- Produced from High Purity Virgin Metals
Available Models
AIM Electropure Reduces Dross Better Than Competitors
Dross Comparison of AIM Electropure Bar vs. Competitors
500 pounds of each type of alloy was heated in a wave solder pot at 500°F for 6 hours. The pot was de-drossed every 3 hours. After 6 hours the amount of dross generated from each type of solder was weighed. AIM’s bar solder has proven to reduce drossing as compared to competitive brands.

News
AIM’s REL22™ Awarded Circuits Assembly’s NPI Award 2018
Cranston, Rhode Island USA – AIM, a leading global manufacturer of solder assembly materials for the electronics industry, announces that their REL22™ high reliability solder alloy was awarded Circuits Assembly’s New Product Introduction (NPI) Award 2018 at IPC Apex at the San Diego Convention Center.
Selected by an independent panel of industry experts, the Circuits Assembly NPI award winner is selected based on creativity & innovation, compatibility with existing technology, cost effectiveness, expected reliability, performance, and more.
AIM’s REL22 lead-free solder alloy is specifically engineered as an exceptionally durable alloy for extreme service environments and provides superior thermal cycling performance and lower voids versus other lead-free alloys. It has been shown to reduce tin whisker formation and improved strength versus SAC alloys making them ideal for high reliability electronics applications.
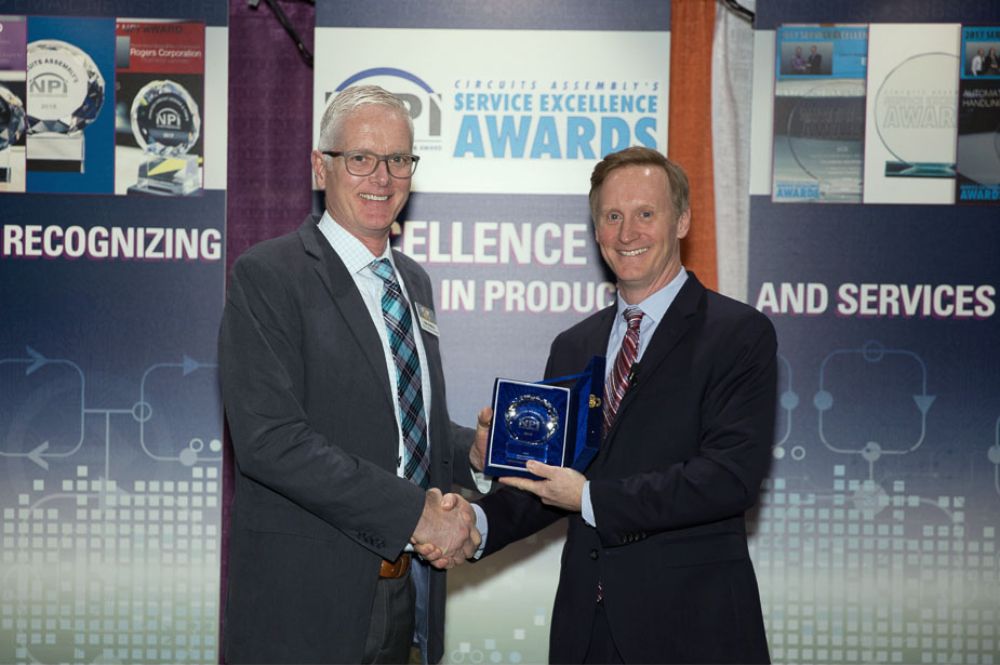
Q&A Sessions – Deep Dive Into the Alloys
High Reliability Alloys and REL22
Discussion about the benefits of using alternative alloys such as REL22™ over SAC305 for high reliability applications. Featuring Tim O’Neill, AIM’s Director of Product Management and Jen Fijalkowski, AIM’s Technical Marketing Engineer.
SAC305 and Alternative Alloys
Tim O’Neill, AIM’s Director of Product Management, discusses the advantages and disadvantages of SAC305 and alternative alloys.
Key Industries
- Semiconductor, Solar & Electronics
More Products
AIM Solder is a leading global manufacturer of solder assembly materials for the electronics industry, catering to various specialized businesses…