Liebherr – Gear Hobbing – LC Series
Is performance-related cutting possible on your machine? As nowadays the economical requirement is more important than ever, modern machines are required.
The Liebherr series LC ensures reliable processing of the required torques and cutting forces. The capability of modern CNC-Gear hobbing machines is emphasized herewith. Quality requirements such as accuracy, stability and temperature resistance are fulfilled with this machine concept. Stable processes are realized during pre- and finish hobbing.
Key Features
- The compact concept requires 20% less floor space. The proven advantages of the integral loader and part storage system are also available with this machine.
- Significantly increased axis and spindle speeds improve productivity and permit more complex machining processes such as roughing, finishing and chamfering with distinct tools in one setup.
- The tool spindle speed maximum of 7000 RPM allows cutting speeds up to 1700 m/min.
- Table speeds up to 1400 RPM enable the use of high number multi-start hobs to reduce cutting time.
- The workpiece loading time of the highspeed swivel loader for wheels up to 60 mm has been reduced to 1.4 seconds, resulting in a chip-to-chip time of less than 3 seconds. The more flexible ringloader enables a chip-to-chip time of 4.4 seconds.
Available Models
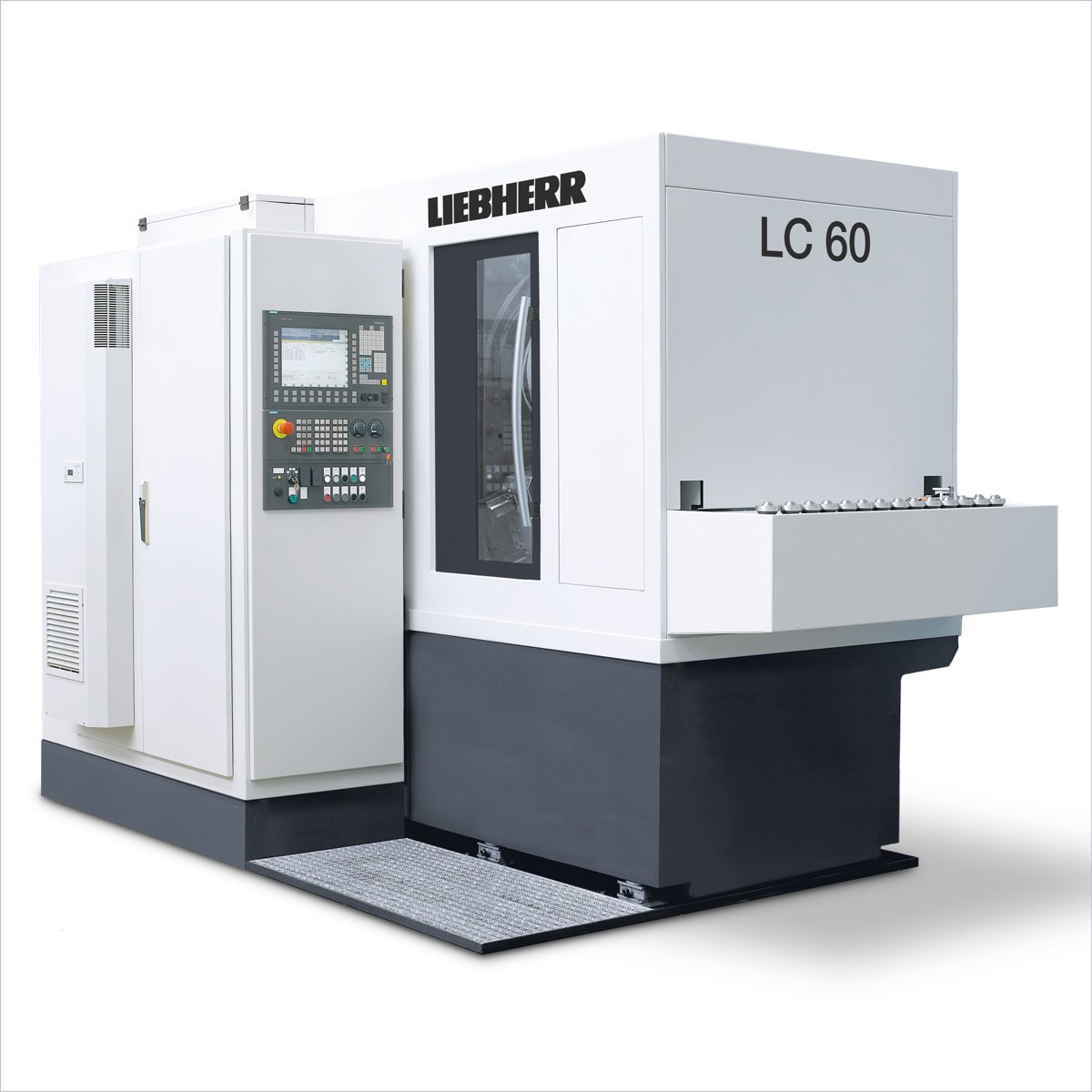
Technical Specifications
Model Name | LC 60 / LC 100 / LC 130 |
---|---|
Max. workpiece diameter (mm) | 60 / 100 / 130 |
Max. nominal module for steel (mm) | 2.75 |
Hob slide travel (axial) (mm) | 200 |
Table diameter (mm) | 125 |
Table speed (rpm) | 1,400 |
Center distance hob/work table (min. mm) | 10 |
(max. mm) | 150 |
Hob head swivel angle (degrees) | +/-45 |
Max. shift travel (mm) | 160 |
Max. hob diameter (mm) | 80 |
Max. hob length/max. toothed length (mm) | 285/190 |
Rapid traverse, axial (mm/min) | 7,500 |
Rapid traverse, radial (mm/min) | 10,000 |
Rapid traverse, tangential (mm/min) | 15,000 |
Rapid traverse, A-axis (°/s) | 30 |
Hob spindle speed (rpm) | 7,000 |
Drive power, hob spindle (kW) | 15 |
Weight of machine with tailstock column (Approx. kg) | 10,000 |
Key Features
- The compact concept requires 20% less floor space. The proven advantages of the integral loader and part storage system are also available with this machine.
- Significantly increased axis and spindle speeds improve productivity and permit more complex machining processes such as roughing, finishing and chamfering with distinct tools in one setup.
- The tool spindle speed maximum of 7000 RPM allows cutting speeds up to 1700 m/min.
- Table speeds up to 1400 RPM enable the use of high number multi-start hobs to reduce cutting time.
- The workpiece loading time of the highspeed swivel loader for wheels up to 60 mm has been reduced to 1.4 seconds, resulting in a chip-to-chip time of less than 3 seconds. The more flexible ringloader enables a chip-to-chip time of 4.4 seconds.
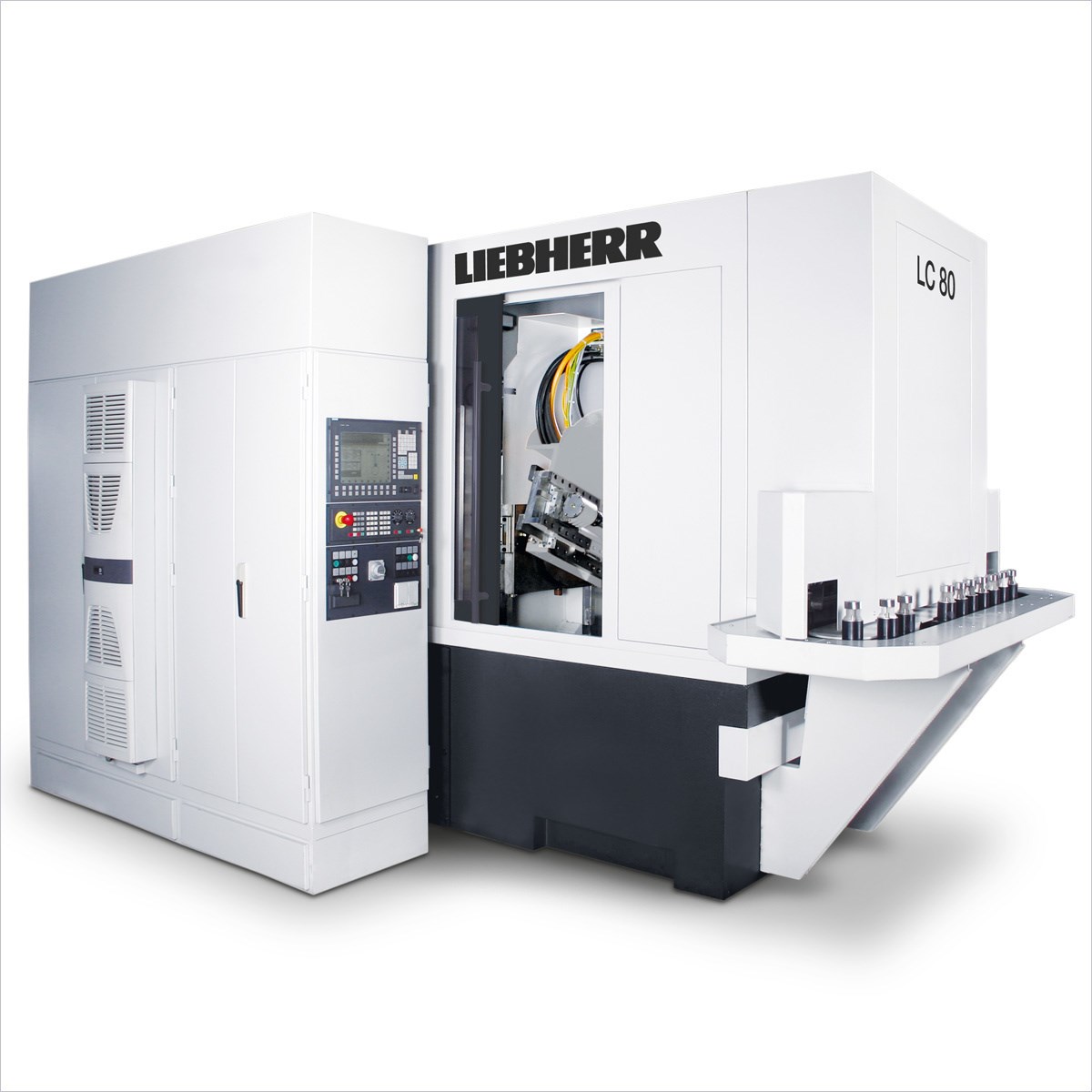
Technical Specifications
Model Name | LC 80 / LC 120 / LC 150 / LC 180 |
---|---|
Max. workpiece diameter (mm) | 80 / 120 / 150 / 180 |
Max. nominal module (mm) | 3(5) |
Workpiece weight (kg) | 15 |
Max. workpiece length (manual loading) (mm) | -50 … +450 |
Max. hob slide travel (axial travel) (mm) | 250/400 |
Table diameter (mm) | 145 |
Table speed (min-1) | 150/250/800 |
Drive power of table (kW) | 5.8/19.0 |
Center distance hob/work table (min. mm) | 10 |
(max. mm) | 200 |
Hob head swivel angle (degrees) | +/-45 |
Hob arbor main bearing | Cylindrial, HSK, SK |
Max. shift travel (mm) | 180 |
Max. hob diameter (mm) | 90 |
Max. hob length (mm) | 220 |
Max. Hob speeds (min-1) | 1,000/1,500/2,000/3,000/6,000 |
Driving power hob spindle (kW) | 15/23 |
Weight of machine with tailstock column (ca. kg) | 10,000 |
Total connected load (ca. kVA) | 25-35 |
Key Features
- Optimised stiffness of the machine bed with FE Analysis model
- Thermo-symmetrical machine design for constant high quality
- Safe and problem-free removal of chips
- High flexibility for different processes: Gears, shafts, worm gears; Cluster gearing; Skiving; Positioned/Oriented gear teeth
- Wet and dry processing
- Hook-ready machine with compact floor space suitable for straightforward implementation
- Chamfer/Deburring in the working area
- The new, user-friendly LHGe@rTec® interface makes it much easier to operate the gear cutting machine and has many advantages for the operator
- Regenerative drive technology
- Use of efficient control cabinet chillers
- LED lighting
- Coolant supply and treatment with speed-controlled pumps
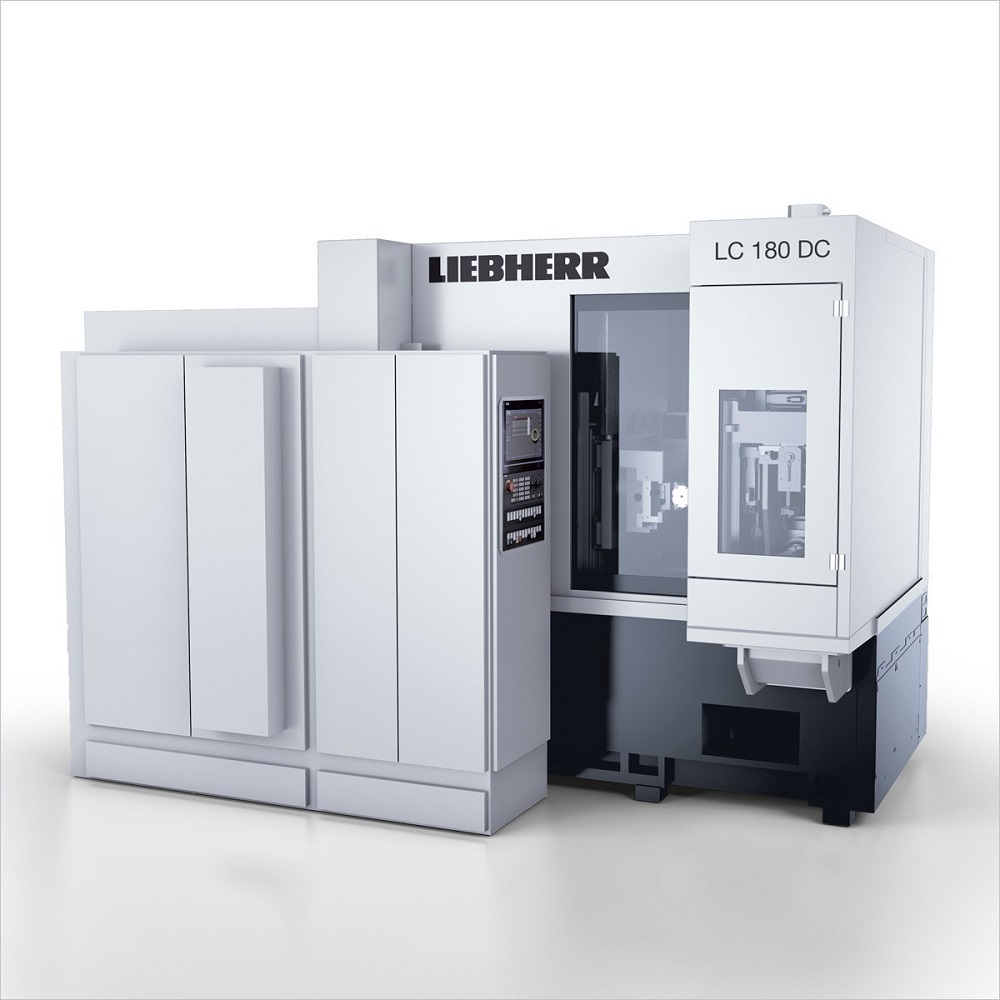
Technical Specifications
Model Name | LC 180 DC |
---|---|
Max. workpiece diameter (mm) | 180 |
Max. nominal module (mm) | 3 |
Axial travel (mm) | 250 / 400 |
Max. shift travel (mm) | 180 |
Max. hob diameter (mm) | 90 |
Clamp length (mm) | 213 |
Max. Hob speeds (min-1) | 6000 |
The great advantage of the LC 180 gear hobbing machine with the new separate Chamfer Cut unit is the simultaneous chamfer in a second machining position – two machines in one, so to speak. The LC 180 DC combines high chamfer quality with single-cut machining. After gear hobbing in the customary single-cut strategy, additional precise and repeatable chamfers are created with the appropriate chamfer cutter, and that with maximum economied performance.
Key Features
- Simultaneous chamfering in a second machining position
- High chamfer quality with single-cut machining
- HSK 50 interface for chamfer spindle: Simple set-up by clamping the cutter onto a an arbor
- No need to shorten the hob length
- Separate fixture for hobbing and chamfering (Stiffness-optimised clamping for hobbing; Collision-optimised clamping for chamfering)
- Without bulging or secondary burrs
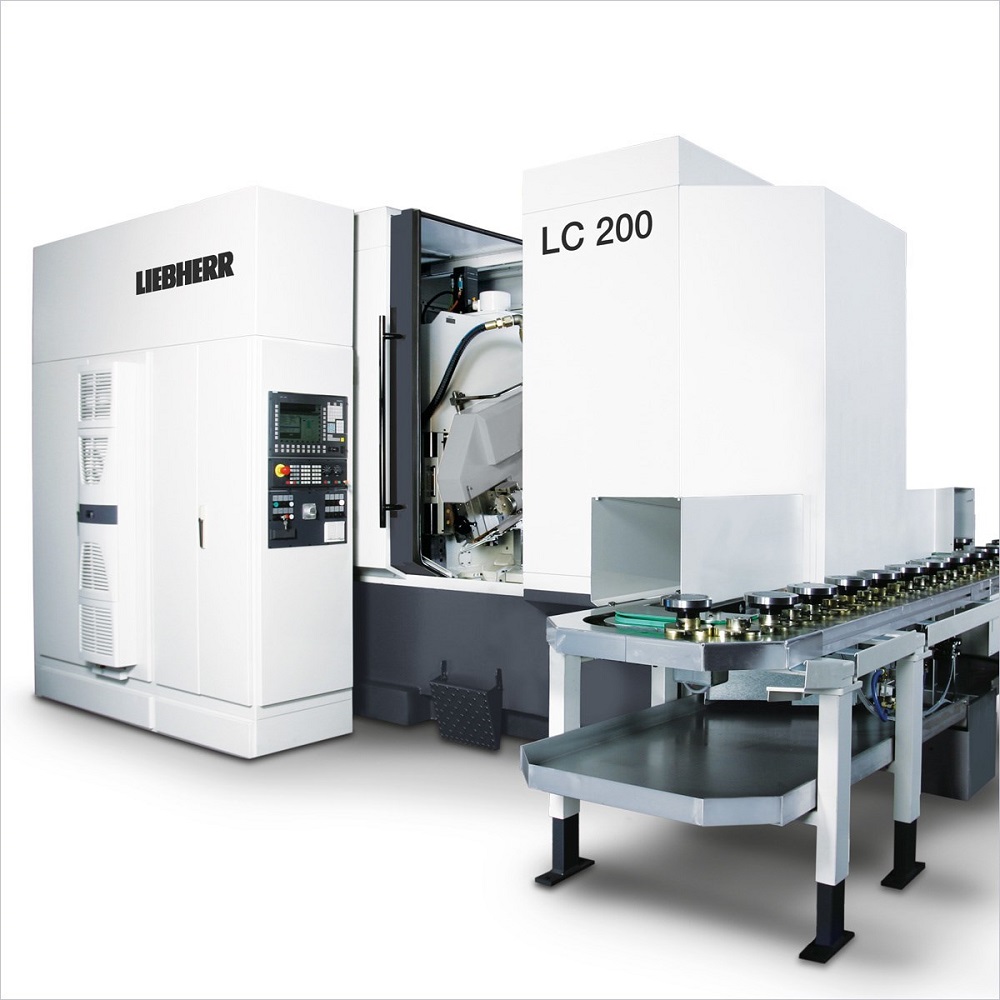
Technical Specifications
Model Name | LC 200 / LC 300 / LC 380 / LC 500 |
---|---|
Max. workpiece diameter (mm) | 200 / 300 / 380 / 500 |
Max. nominal module (mm) | 7/12 |
Workpiece weight (kg) | 100 |
Max. workpiece length (manual loading) (mm) | 680 (1,200) |
Max. hob slide travel (axial travel) (mm) | 600 |
Table diameter (mm) | 180 / 250 / 320 / 320 |
Table speed (min-1) | 100/200/400 |
Drive power of table (kW) | 5.56/11.8/15.0 |
Center distance hob/work table (min. mm) | 15 |
(max. mm) | 400 |
Hob head swivel angle (degrees) | ± 35/45 |
Hob arbor main bearing | Cylindrial, HSK, SK |
Max. shift travel (mm) | 200/300 |
Max. hob diameter (mm) | 160/220 |
Max. hob length (mm) | 230/330 |
Max. Hob speeds (min-1) | 500/750/1,500/3,000 |
Driving power hob spindle (kW) | 14/27 |
Weight of machine with tailstock column (ca. kg) | 16,000 |
Total connected load (ca. kVA) | 35-50 |
Key Features
- 6 CNC axes
- Optimised stiffness of the machine bed with FE Analysis model
- Thermo-symmetrical machine design for constant high quality
- Safe and problem-free removal of chips
- Wet and dry processing
- High flexibility for different processes: Gears, shafts, worm gears; Cluster gearing; Skiving; Positioned/Oriented gear teeth
- Hook-ready machine with compact floor space suitable for straightforward implementation
- Hand or machine-internal crane loading
- Chamfer/Deburring in the working area
- The new, user-friendly LHGe@rTec® interface makes it much easier to operate the gear cutting machine and has many advantages for the operator
- Regenerative drive technology
- Use of efficient control cabinet chillers
- LED lighting
- Coolant supply and treatment with speed-controlled pumps
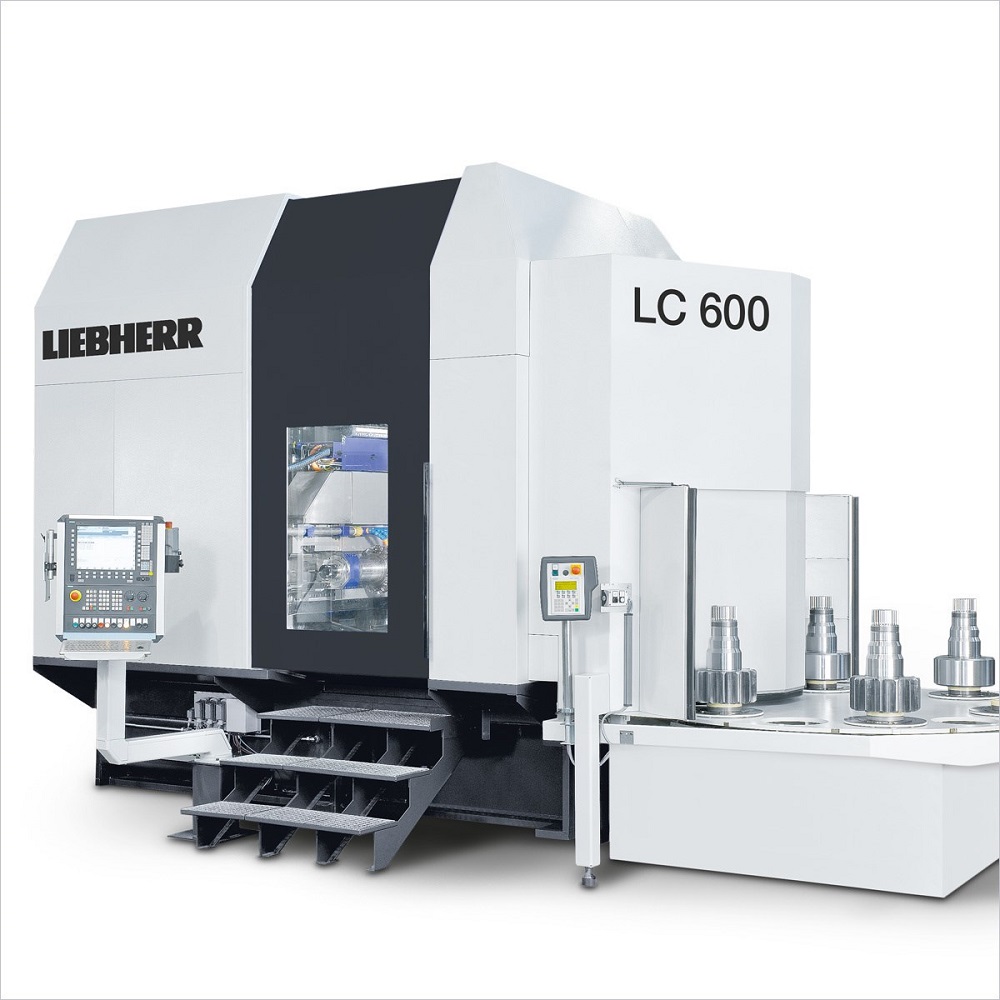
Technical Specifications
Model Name | LC 600 / LC 700 / LC 800 / LC 1000 / LC 1200 / LC 1400 / LC 1600 / LC 1800 / LC 2000 |
---|---|
Max. workpiece diameter (mm) | 600 – 2000 |
Max. nominal module for steel (mm) | 16-24 |
Max. hob slide travel (mm) | 1000-1400 |
Table diameter (mm) | 525 – 1200 |
Table speed (min-1) | 10-80 |
Center distance cutter/table (min. mm) | 50-180 |
(max. mm) | 440-1300 |
Hob head swivel angle (degrees) | ± 35-45 |
Hob arbor main mounting | SK 45/HSK-A 80; SK 50/HSK-A 100 |
Max. shift/tangential travel (mm) | 220-320 |
Max. hob diameter (mm) | 210-450 |
Max. hob length (mm) | 260-605 |
Cutter speeds (min-1) | 375/500/750/1.000; 275/360/450/600 |
Drive power – cutter spindle (kW) | 30-45 |
Machine weight with tailstock column (appr. kg) | 21,000-26,500 |
Total connected power (max. kVA) | 65-80 |
For the development of this machine series the characteristics of the very successful new machine generation from Liebherr was systematically transferred to the application of the universal machines LC 600 – LC 2000. The necessary flexibility for different applications is achieved with a two-piece machine bed. With this concept the machines can be optimally configured to customer specific requirements. The self-supporting, very rigid design permits a machine installation directly on the floor, without a special foundation. Chip removal is accomplished through the machine bed with the main chip conveyor arranged lengthwise. The machine bed and laterally arranged coolant tanks hold approx. 800 l of coolant.
Key Features
- Maintenance-free, high-dynamic AC drive technology with different ratios for the backlash-free cutter drive provide the torque required for high performance cutting, at spindle speeds up to 1000 rpm and up to 45 kW. The hob arbor mounting can be with hollow shaft taper (HSK) to DIN 69893 or with ISO taper.
- Dual worm wheel drives or direct drives are used for a backlash-free table drive. The table spindle is equipped with hydrostatic radial and axial bearings for high table loads, up to 60/95/120 kN and maximum radial rigidity. The water cooled AC table drive ensures highest accuracy and reliability. Large table bores accommodate hydraulic clamping cylinders for actuating workpiece clamping fixtures.
- PC based control technology
- Digital drive technology
- Integrated PLC
- Advanced field bus systems (profi bus)
- TFT flat screen
- Optional network integration
- Dialog input tailored to gear machining
- Teleservice
- Diagnostic tools
- Workpieces up to 800 mm diameter can be automatically loaded and unloaded with a 2-station ringloader. Parallel grippers with adjustable diameter range are used for a large part variety.
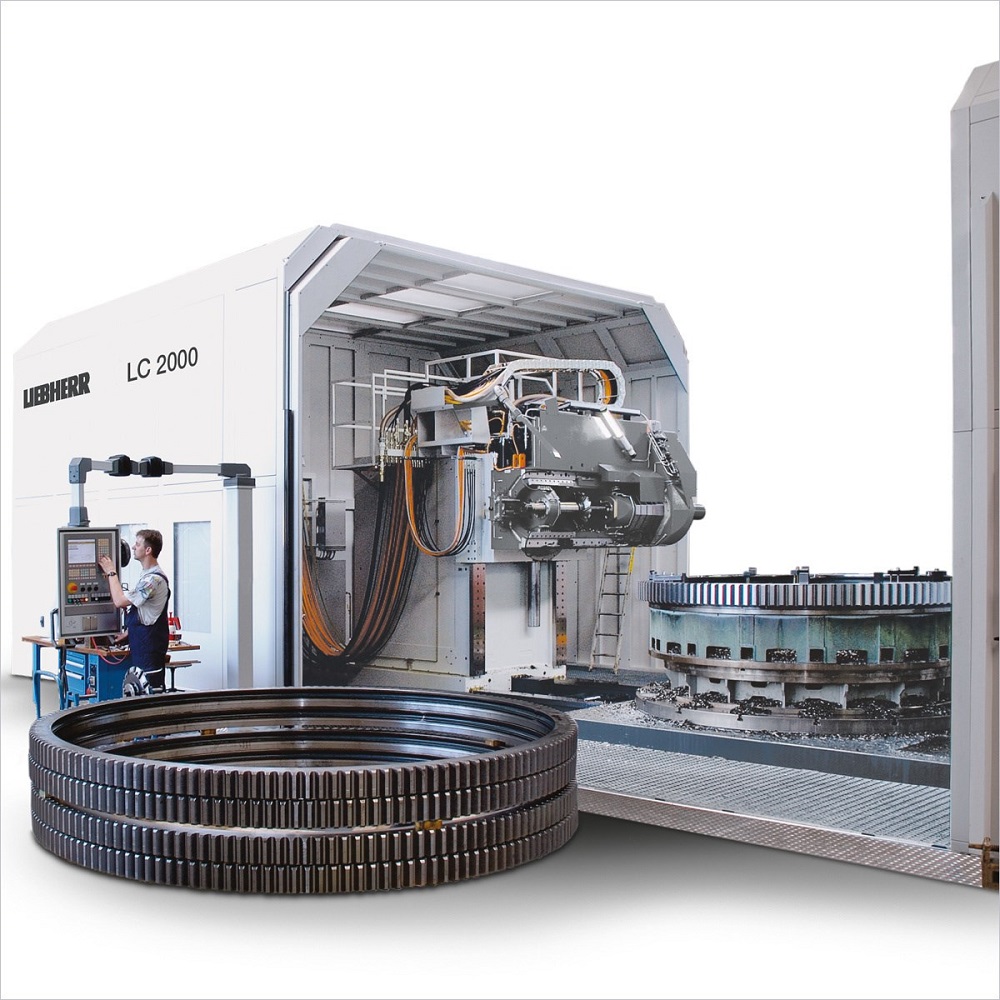
Technical Specifications
Model Name | LC 2000 / LC 2500 / LC 3000 / LC 4000 / LC 6000 / LC 8000 / LC 10000 / LC 12000 / LC 16000 |
Max. workpiece diameter (mm) | 2000-16000 |
Max. nominal module during hobbing/profile milling (mm) | 24-100 |
Hob slide travel (mm) | 1200-2400 |
Lowest hob head pos. above table (mm) | 600-900 |
Table load (kN) | 200-2000 |
Table bore continuous (mm) | 500-1500 |
Max. hob head swivelling angle (degrees) | +/- 45° |
Max. shift travel/tangential travel (mm) | 300-700 |
Max. hob diameter (mm) | 320-650 |
Max. hob length (mm) | 440-900 |
Hob speeds (min-1) | 150-250 |
Drive capacity hob spindle (kW) | 53-120 |
Total connected load (kW) | 125-320 |
Key Industries
- Machinery & Manufacturing
Liebherr-Verzahntechnik GmbH, founded in 1969, is one of the leading manufacturers of machine tools and automation systems. The company offers…
-
SINGAPORE
DKSH Singapore Pte Ltd 625 Lorong 4 Toa Payoh, #03-00 319519 Singapore Singapore
+65 6274 1222
+65 6273 1503
-
THAILAND
DKSH (Thailand) Limited 2106 Fantree 4 Building Sukhumvit Road, Phrakhanong Tai, Phrakhanong 10260 Bangkok Thailand
Download now
How to Disable Pop-Up Blockers for Smooth Downloads
Google Chrome (Version 110 and later):
- Click the three dots (menu) in the top-right corner and select Settings.
- Under Privacy and Security, click Site settings.
- Scroll down to Content and click Pop-ups and redirects.
- Toggle the switch to Allowed or add https://technology-products.dksh.com to the Allow list.
Mozilla Firefox (Version 90 and later):
- Click the three horizontal lines (menu) in the top-right corner and select Settings.
- Go to the Privacy & Security section.
- Scroll to Permissions and uncheck Block pop-up windows for https://technology-products.dksh.com.
Microsoft Edge (Version 110 and later):
- Click the three dots (menu) in the top-right corner and select Settings.
- Scroll down to Cookies and site permissions.
- Under Site permissions, click Pop-ups and redirects.
- Toggle the switch to Allow or add https://technology-products.dksh.com to the Allow list.
Safari (Version 14 and later):
- Open Safari and go to Preferences (from the top menu).
- Select the Websites tab.
- Under Pop-up Windows, select Allow for https://technology-products.dksh.com.